Tech Notes: Preventive Maintenance Goes a Long Way in Keeping Application Equipment Operating
Preventive maintenance is one of those things that just doesn’t happen in most cases. Just ask my wife. I don’t practice what I preach around the house.
For custom applicators and farmers, downtime is very costly. When I started Agri-Tech in 1985, my mission was to service control systems that were showing up on all the new machines in the custom application business.
There were hundreds of spreaders and sprayers in the three states in which I was working, most equipped with Dickey-john DG60 and 215 Series spray controllers. No digital displays. Loud beepers went off, telling operators that something was wrong while offering no clues as to what. Speed sensors were installed in the speedometer line to measure ground speed through rotation of the speedometer cable.
Preparing for this column was a lot like a trip in the way-back machine as I visited Wollam Ag Center in Continental, OH. The company is a great family-owned retailer and applicator, one that was never into buying the latest new rig. It took care of what it owned and built much of the new equipment itself.
It was a treat visiting Wollam, and, sure enough, it had lots of examples of where preventive maintenance could be in order.
Cable Inspection
Most of the machines out there use controllers that have been retrofitted over the years with different controllers. Many times they are installed by guys who really don’t understand the environment in which they are used.
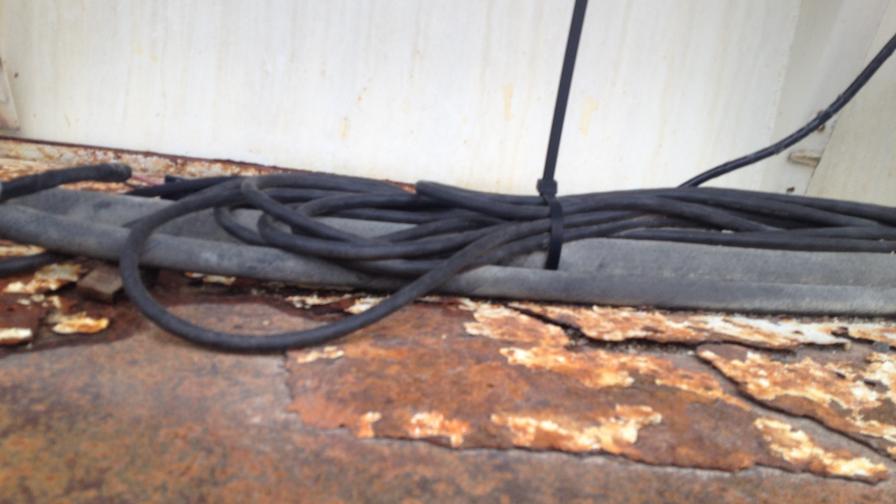
The first step in preventative maintenance is to take care of the cabling.
The first step in preventive maintenance is to take care of the cabling. I used to, as part of my program, actually touch and flex every inch of the cable. Doing that forces you to find nicks and scrapes on the cables. Little nicks in a cable can shut the machine down once corrosion starts. Re-tie all the cables after the inspection, and you should be good.
Check and Dispose of Bad Connectors and Quick Fixes
Over the years many quick fixes are used to get a machine back in the field with the plan to later fix it correctly. Later never comes, and you don’t think about it until the machine quits again in the field. Take the time to FIX IT RIGHT. Believe me, wire nuts are not meant to be a long-term fix on a machine exposed to the environment of a fertilizer rig.
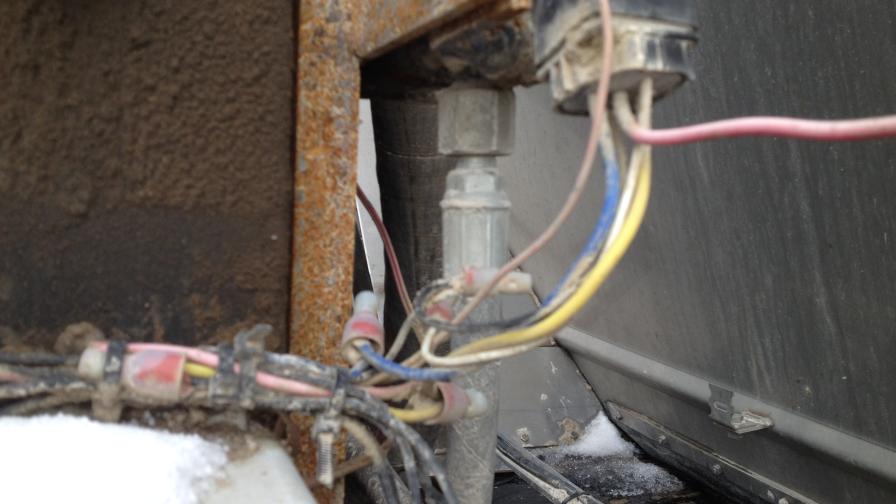
Be sure to check and dispose of bad connectors and quick fixes.
Pull the connectors apart and closely inspect the pins. Use contact cleaner to clean them, and then protect them with a non-conductive grease.
Software Updates
I have never been a fan of doing software updates unless there is a problem that the update hopes to fix. The problem with the update is that it may affect all of the pieces involved in the system. When the rig hits the field, it doesn’t work because the modules also need upgraded.
Don’t do the upgrade unless you are in a position to fully run the machine before you call the upgrade done. Many times through the reboot process little things, such as calibration numbers, are set back to defaults. The display looks good, but the rates are off.
Speed Sensors
I wanted to include this photo below, which shows two problems getting ready to cause trouble. The rig needs some cable ties, but it is also still using the Dickey-john radar that was probably installed 25 years ago.
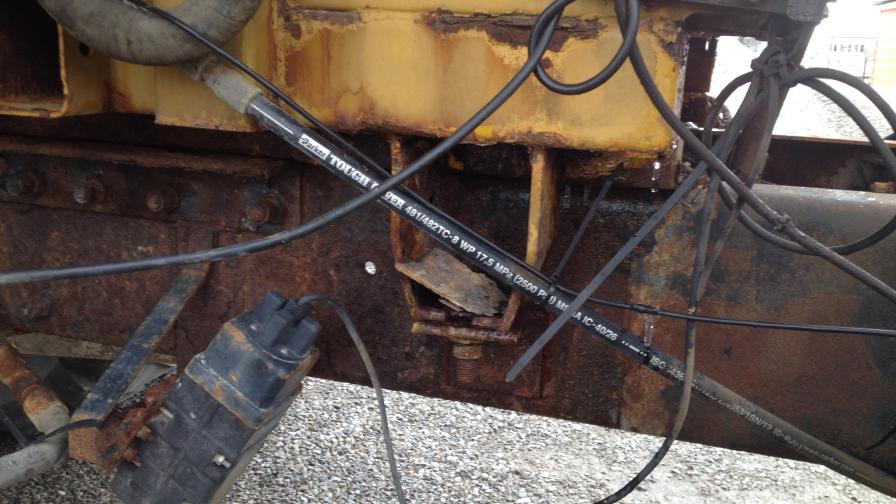
The rig needs some cable ties but it is also still using the Dickey-john radar that was probably installed 25 years ago.
These were on all the early machines. This one is on the wrong angle, so it won’t calibrate as normal, although it will still work. Don’t bother with the angle, because the bracket will fall apart.
Today and for the last 10 or more years, speed input is provided by the GPS receiver or a dedicated GPS to substitute for radar. The system speed will use a calibration number for set-up. They still need to be checked, especially after a software update.
Product Distribution: Dry Spreaders
Back in the days before precision ag, we used to do any job related to the proper distribution of the material across the spread or spray application width. That meant with air spreaders we actually hung bags on the drops and measured the amount of material at each spot. With spinner spreaders it was pan testing.
The first rule with dry spreaders is that they MUST BE CLEAN! The job of the product drop control is to correctly place the product of the spreader disk. Then the correctly adjusted blades will throw the material where it belongs in the spread pattern.
Believe me, please: When product is built up on the blades, the pattern is not right. Take the time to clean things up. You can buy test pattern kits from your dry-box supplier.
The couplers on rate sensors can get loose. When that happens, the rig will appear to work, but the rates become very erratic. Take a quick look to verify that the sensor is tight on the shaft.
Product Distribution: Liquid Machines
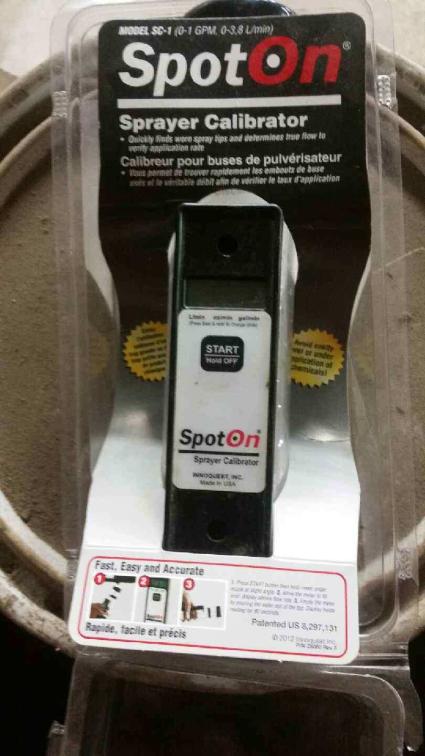
Using SpotOn is an easy to test flow.
Liquid machines also have product distribution across the application width as a concern. With electronic controllers the gallon counters built into the system should be accurate. If the display says you sprayed 965 gallons, that should be correct.
That’s the overall product delivered to the boom. The big question becomes, where is it going across the boom? Catch testing is the only good way to know where the flow is going.
Years ago catch testing was complicated. You needed calibrated containers and accurate timing. Then you did the math to calculate the flow rate checking each nozzle. Catch testing will find partially closed valves, crimped hoses, bad nozzles, and plumbing errors.
SpotOn has a test unit that, I am told, is the easy way to test flow. It’s all automatic. Catch testing is worth the effort. Your customers will appreciate the accuracy. Contact your spray nozzle supplier to check out the SpotOn unit.
I hope you have found this Tech Notes column to be useful. Have a safe and accurate and trouble-free season.
Please take a minute to check out my website, agtester.com, for tools for the ag technology specialist. I appreciate your feedback. Remember, Tech Notes is for the field guys. Please pass it on!