In-Plant Equipment and Systems Become Critical for Ag Retailer Success
The pace of change in the ag industry can, at times, be overwhelming. The products growers use constantly undergo innovation, improving yield and profitability. Along with that the tools used to store and handle those products — including in-plant equipment and systems — must be upgraded as well.
“Commodities are now stored in state-of-the-art conditioned dry sheds or stainless tanks,” says Bob Fitzpatrick, Segment Manager-Global Product Management, Fertilizer Systems, AGI Fertilizer Systems. “The best dry sheds utilize non-corrosive building materials and heated floors to reduce humidity and increase workplace safety.”
Those advances along with a few other factors have made in-plant systems critical.
“Thanks to consolidation and increased competition, in-plant systems have become a necessity for ag retailers and wholesalers looking to stay competitive,” says Todd Scobie, Murray Equipment Inc. (MEI) Sales and Marketing Director, ICS. “The speed, accuracy, and customer service advantages of in-plant systems are so clear that ag retailers and wholesalers recognize that their longevity is tied to in-plant equipment and systems.”
Kahler Automation Marketing Manager Chuck Schrader, agrees.
“The recent trend of mergers and acquisitions highlights the value to be captured with automation,” he says. “With centralized agronomy hubs managing larger inventories, precision is no longer a luxury, it’s now a necessity.”
A Changing Market for In-Plant Equipment
“Equipment safety has become a core principle in AGI product designs. In addition, as part of this focus, AGI continues to improve ease of equipment maintenance for their customers,” Fitzpatrick says.
Key is getting that software and the hardware to work together seamlessly.
“In the past decade, in-plant systems took a software-first decision-making approach when deciding which in-plant system they wanted to use,” Scobie says. “Today, retailers recognize that synergies between the equipment and software and controls are key to achieving production and customer service goals.
“Also, the accessibility of high-speed internet has allowed for software features such as improved multi-location management, online support, and web-based options,” MEI’S Scobie says.
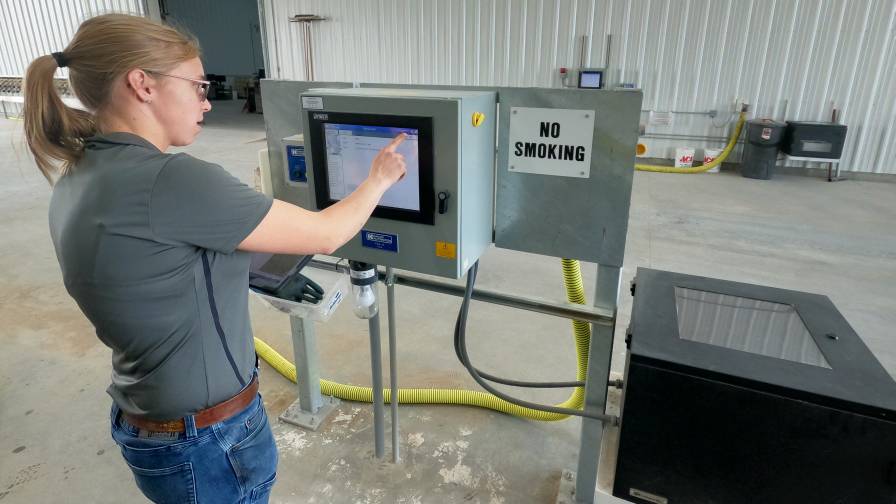
In-bay controls allow drivers to start and pause orders get notified when an air purge completes the load out. Photo Credit: Kahler Automation
When they work well, in-plant equipment and systems save companies time and money.
“Automation is now being viewed as an essential instead of a differentiator,” Kahler’s Schrader says. “With labor and supply issues being felt across the industry, accurate and efficient processes are vital to retailers’ success.”
In-Plant Equipment Segment Drivers
No matter how good a system is, it needs to provide measurable ROI or it’s not likely to find many users.
“Customers are demanding higher value in their blending systems with strong financial payback reflected in equipment durability, longevity, and ease of use,” AGI’s Fitzpatrick says.
According to MEI’s Scobie, “Consolidation and increasing competition along with rising inventory costs are driving ag retailers to update their facilities with the latest in-plant technology.”
Mark Mohr, Vice President of Sales and Marketing, Kahler, points to a trio of factors pushing the growth of in-plant systems — more products, better business controls, and less labor.
“The farmer’s agronomy toolbox seems to be always expanding, requiring facilities to handle more biologicals, micronutrients, and proprietary blends that just were not mainstream 10 years ago,” Mohr says. “Add to that the business acumen and close tracking of inventory it takes to run a financially efficient business now, and the limited labor force in most of rural America, and the drivers for automation are extremely strong.”
2024 and Beyond
“The expectation is that the fertilizer blending segment will continue its growth trend as more customers revitalize existing facilities and expand to serve their customer base,” AGI’s Fitzpatrick says. “We expect substantial growth in the developing regions as they focus on increasing food production through custom fertilizer blends.”
As good as these systems are, like any mechanical device, at some point it will need to be replaced.
“As facilities age, we will see more and more retailers updating their in-plant systems, ICS’s Scobie says. “We are also involved in a lot of new facilities as retailers are looking to expand into new markets and take control of their inventory company wide. With inventory and commodity prices, retailers and wholesalers are finding value in shared inventories across regions.”
As agriculture becomes more technologically advanced, in-plant systems must keep pace.
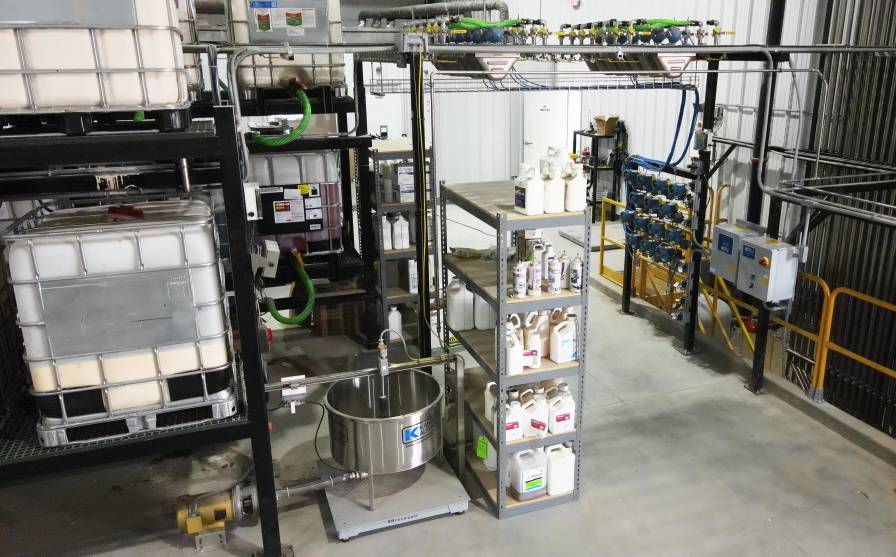
Mass flow system for micro high speed loading of complex micro system blends. Photo Credit: Kahler Automation
“This is a strong time for upgrading and adding capabilities,” says Kahler’s Mohr. “Most facilities built in the past 15 years were designed with expansion in mind, whether more products or more bays.
“Just like the industry moved from the local facility that handled maybe five railcars of fertilizer, to the regional supply hubs handing unit trains and many dozens of trucks, the future is going to be about efficient logistics,” Mohr continues. “This doesn’t always mean bigger. We see the future being more connected to be more efficient be connecting regional facilities together to act like super-facilities. Farmers are consolidating also, and many interact with two or three of their ag retailer’s facilities already.”
Regarding the necessity of in-plant systems, Kahler’s Schrader puts it simply: “The recent trend of mergers and acquisitions highlights the value to be captured with automation. With centralized agronomy hubs managing larger inventories, precision is no longer a luxury, it’s now a necessity.”