In-Plant Equipment and Systems: How Manufacturers Are Offering Sophisticated Solutions That Are Still Easy to Use
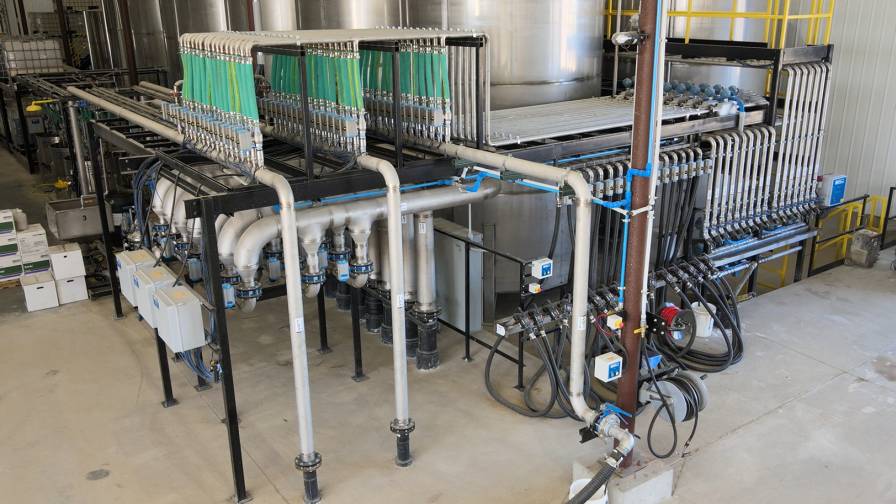
In-bay controls allow drivers to start and pause orders get notified when an air purge is complete. Photo: Kahler Automation
Like many of the tools used by growers and ag retailers, in-plant equipment and systems have become more sophisticated and help manage a variety of issues. The increased complexity also comes with ease of use, and manufacturers continue to deliver new solutions.
State of the Segment
“Consolidation is an ongoing trend in the industry, with newer plants serving larger geographic areas and replacing smaller, outdated facilities,” says Colt Silvers, Vice President of Business Development, Kahler Automation. “Most facilities constructed in the last decade have been designed with the capability to expand, accommodating more bays or products.”
There are several reasons these systems are increasing in size, not the least of which is that the number of customers they serve is growing.
“Between industry consolidation, higher inventory costs, and labor shortages, in-plant systems have become a necessity for ag retailers and wholesalers who are looking to stay competitive,” says Todd Scobie, Sales and Marketing Manager, Murray Equipment Inc. (MEI). “The speed, accuracy, and efficiency advantages of in-plant systems are so clear that ag retailers and wholesalers recognize that their longevity is tied to in-plant equipment and systems.”
Changing Systems
Automobiles that once only required a bit of mechanical know-how to repair now, seemingly, need an advanced computer engineering degree to understand. Similarly, in-plant equipment and systems have continued to incorporate more sophisticated electronics, but also like cars that doesn’t make them more difficult to operate.
“Today, retailers recognize that synergies between the equipment and software and controls are key to achieving production, customer service, and inventory management goals,” MEI’s Scobie says. “Both MEI equipment and controls work hand-in-hand to for a seamless experience.
“The increasing availability of high-speed internet has allowed for software features such as improved multi-location management, online support, and network-based options,’ Scobie continues. “MEI’s ICS Controls, which can control both liquid and dry fertilizer operations, offers these capabilities to retailers and wholesalers.”
Ease-of-operation is critical as labor continues to be a challenge across the ag supply chain.
“The ongoing trend of delivering more with fewer locations and reduced staff is evident,” says Kahler’s Silvers. “Retailers now need to accommodate an expanded range of products, including biologicals, micronutrients, and proprietary blends that were not mainstream a decade ago. Efficient business management, particularly inventory control, is vital for financial success.”
There are a number of factors driving those changes. Silvers outlines a few of the major motivators.
“Workforce availability, a rise in product diversity, and improved business controls are key drivers,” he says. “The limited labor force in many rural areas underscores the necessity for automation. Growers must adapt to maximize their ROI, exploring different combinations of crop protection options. This expansion in options places additional demands on retailers.
MEI’s Scobie echoes that sentiment.
“Turnover and labor shortages have been a pain point for ag retailers in recent years,” he says. “At MEI, we’ve focused on making our in-plant systems intuitive, accurate, and safe. We offer several HMIs (human machine interfaces) so users can access the systems from tablets, control boxes, and computers. This allows users to effectively be in multiple places at the same time. We’ve also seen an uptick in unattended solutions. This allows inventory to be moved round the clock and eases the burden on plant staff requiring less overtime and increasing throughput during the day.
Looking Ahead
“As facilities age, we will see more and more retailers updating their in-plant systems,” MEI’s Scobie says. “We are also involved in a lot of new facilities as retailers are looking to expand into new markets, take control of their inventory company-wide, and simplify procedures for less experienced employees.”
Like other tools, in-plant equipment and systems must integrate with other office tools to maximize efficiency.
“With larger centralized agronomy hubs becoming more commonplace, optimizing logistics will be very important,” Kahler’s Silvers says. “In response, our Load Optimizer feature enables operators to efficiently organize orders, prioritizing based on geographic region, tender, applicator, and more. This ensures that trucks are filled to capacity with the highest priority orders, promoting efficiency and accuracy in order fulfillment.”
There are plenty of opportunities for growth, Silvers continues.
“Accurate and efficient processes are pivotal to retail success,” he says. “A growing demand for data-driven products reflects a broader trend. Customers are looking for solutions that offer dashboards and analytics at the organizational level, enhancing visibility and providing valuable insights to management.”
As retailers expand their reach, the latest in-plant equipment and systems work together so an operation spread over multiple sites is easily managed.
“With inventory and commodity prices, retailers and wholesalers are finding value in shared inventories across regions,” MEI’s Scobie says. “By converting to ControlPro Central HUB, it allows all of a company’s locations and the home office to work in unison. At MEI, we’ve built our 70-plus year business on helping solve the real-world challenges of our customers. We approach every industry challenge as an opportunity to improve our customers’ businesses by applying innovative engineering and next-gen software development.”
Company Offerings
Kahler Automation: “Constellation is an enterprise solution that allows customers to standardize data management for all locations at the organizational level, and providing increased visibility to managers with an easy-to-use reporting dashboard,” Silvers says.
“We also recently introduced LOADPASS, an app that provides drivers with an easy mobile check-in for shorter lines at the terminal, and contactless loadout for increased efficiency. The system is adaptable to meet various site requirements, including the need to scale trucks, capture signatures, and other customizable options.”
Murray Equipment Inc.: “One benefit to MEI’s ICS Controls is that we continually push out updates,” Scobie says. “Our products evolve with new features being added throughout the year as we partner with customers to help them be more productive.”