Fertilizer Mixing and Blending Systems: How Constant Innovation Is the Driving Force Behind Better Precision
The age of the intelligent machines has begun.
Smart technology and artificial intelligence are finding their way into the tools and devices that power the world. Agricultural tools in general, and blending and mixing systems specifically, are no exception. That’s just one of the trends making these fertilizer-handling operations smarter, more independent, faster, and more efficient.
“The market for agronomy dry fertilizer mixing and blending systems is experiencing several notable trends,” says Nate Reznechek, GSI Sales Director-Fertilizer. “One of these trends is the integration of technology, such as automated systems and software-based management systems, which help optimize blending processes. Another trend is the customization and precision of fertilizer blends to suit specific soil conditions and crop requirements. There is also a growing emphasis on sustainability and environmental concerns, with a focus on creating eco-friendly formulations that minimize environmental impact.”
These trends, Reznechek says, are driven by a variety of factors.
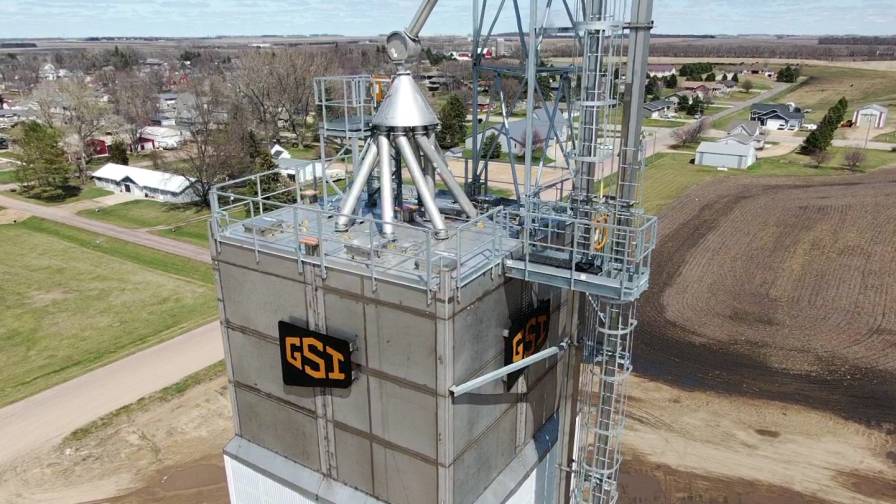
GSI’s advanced blending tower nearly doubles the speed of typical systems, shortening wait times, with blends remaining consistent from batch to batch. In one hour, up to 13 24-ton trucks are safely filled with high-quality, custom dry-fertilizer blends with impregnation.
“Efficiency and scalability are also important factors, with customers looking for systems that offer both speed and accuracy in blending operations, as well as the flexibility to handle varying batch sizes,” he says. “Remote monitoring and data analysis capabilities are becoming more popular, allowing for real-time monitoring and data-driven insights. Collaboration and integration with other agricultural machinery and systems are also important, as it allows for a more holistic approach to farming practices.
Finally, regulatory compliance and safety are critical factors, with users preferring systems that prioritize safety features and adhere to industry standards. These trends collectively reflect the evolving landscape of the agronomy dry fertilizer mixing and blending systems market, where innovation, sustainability, precision, and efficiency are driving forces.”
According to Todd Scobie, Sales and Marketing Manager, Murray Equipment Inc. (MEI), the challenges faced at the start of this decade have led to changes for retailers.
“In recent years, supply chain issues, labor shortages, and continued consolidation have changed the mixing and blending system requirements for retailers. Ag retailers need strategically located storage, intuitive automation, increased loadout speed, and accurate ticket fulfilment and billing procedures.”
A variety of manufacturers offer mixing and blending systems providing retailers with several options.
“The market centers on constant innovation and unique value propositions to establish strong user benefits and overcome operational challenges,” Reznechek says. “Suppliers must differentiate through accuracy, productivity, and flexibility. Collaboration is critical, enabling technology availability and utilization. The shifting landscape stresses distinctive capabilities and technological advances to maintain competitive advantages.”
MEI, the developers of ICS controls, including ICS ControlPro, sees a strong market for mixing and blending systems in 2024 and beyond.
“We expect to continue to see an increase in demand,” he says. “The ROI we can provide when replacing aging facilities and the strategic advantage we can offer to retailers looking to expand their reach, increase capacity, reduce load times, and improve accuracy, makes new blending facilities an easy decision. Just the improvements in inventory management alone, not to mention customer satisfaction, make new mixing and blending systems a no-brainer.
New Technology
The technology introduced into mixing and blending systems improves the ability of end users to better serve their customers.
“Manufactures are rolling out various improvements to enhance the user experience with agriculture mixing and blending systems,” GSI’s Reznechek says. “These include sophisticated sensor technologies for precise measurements, automated processes, and real-time data for adjustable operations. Designs allow for batch flexibility. Remote monitoring and intuitive controls improve usability. At their core, these upgrades seek to streamline functionality and meet user needs while emphasizing accuracy, sustainability, and compliance with regulations.”
Technology quickly transitions from amazing new feature to expectation.
“Automation is becoming standard.” MEI’s Scobie says. “Since innovations are happening daily, we believe we’ll see a transition to controls that can be updated online to add in new functionality. This is a departure from completely replacing software and controls to update the automation. Also, with consolidation and labor shortages, an intuitive common software package across locations is key to taking advantage of economies of scale. Tapping into the inventory across locations, being able to move employees to other locations as needed, and enjoying 24/7 unattended loadout reducing the need for overtime are a few of the benefits of ICS ControlPro.”
Challenges, Opportunities
While the advancements in technology drive interest in new mixing and blending systems, they can also create challenges for manufacturers because customers come to expect continued innovation.
“Going forward, the agronomy industry faces several obstacles,” GSI’s Reznechek says. “These include the constant need for innovation to match changing needs and integrating technology for better precision.”
Other obstacles, Reznechek says, include: “Adapting to changing regulations and environmental factors present continuing difficulties. Scaling up to meet varied farming requirements and promoting sustainability in resource use are major challenges. Also, finding a balance between cost and advanced capabilities remains a persistent hurdle. Effectively managing these challenges will be critical for the industry’s growth.”
MEI’s Scobie shares some additional concerns for retailers.
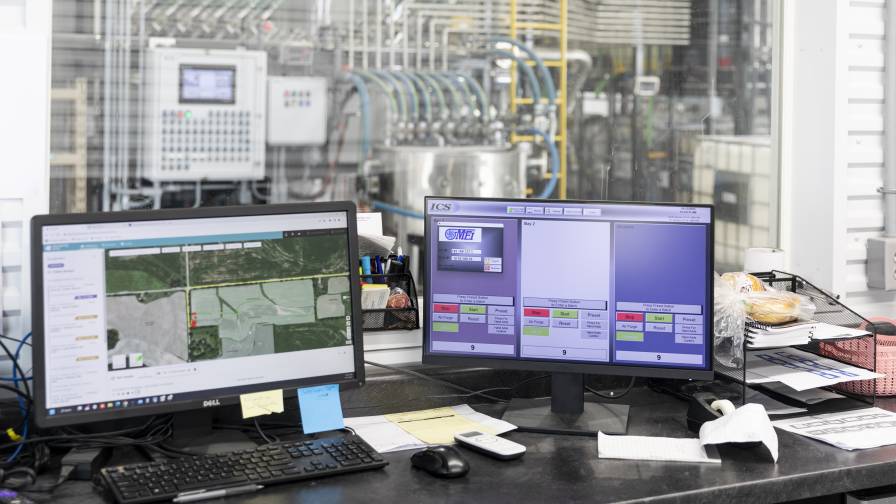
Murray Equipment Inc. ICS Controls seamlessly tie blending systems and facilities to the home office.
“Aging facilities, need for increased throughput, strategic growth plans, and efficiency are why retailers approach MEI to build new systems,” he says. “Speed, efficiency, customer service, safety, and inventory management are the primary drivers for new blending software and automation. Retailers want to serve their growers better by providing more accurate blends and billing in a timelier manner without increasing the demands on their existing staff.
“As growers consolidate and demand higher response times from retailers, it’s companies with fast and efficient blending facilities along with good customer service practices that will stand out,” Scobie continues.
Final Thoughts
“For cooperatives, GSI’s equipment enables improved efficiency and flexibility in serving their members,” Reznechek says. “The technology facilitates customized fertilizer blends to meet the diverse needs of various farmers. This adaptability improves member satisfaction and loyalty while enhancing the cooperative’s offerings. Furthermore, the reliable and efficient equipment optimizes cooperative operations, allowing them to handle large fertilizer volumes smoothly.”
Those key benefits mixing and blending systems provide have become even more critical.
“The issues retailers are facing with supply chain disruptions is initiating discussions with MEI to help them gain more control over their supply,” Scobie says. “Depending on their specific supply issues, business models, and geographic locations, solutions have included expanding storage capacity, improving inventory management, and in some cases expanding the in-house mixing and blending capacity.”