Flashing Back And Moving Forward On Spray Drift
The potential for pesticide drift remains an unavoidable feature of modern agriculture. Here, too, history repeats itself.
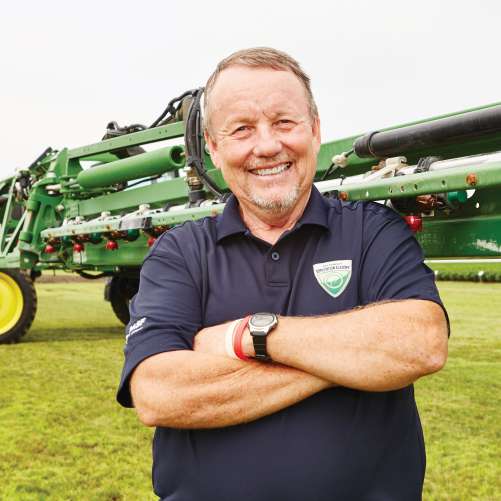
Dr. Bob Wolf trains applicators in BASF’s On Target Application Academy.
“When Roundup debuted, drift was a severe issue,” recalls Dr. Bob Wolf, renowned industry expert on pesticide application. “Twenty years later, everything was Roundup Ready, so nobody worried about it. Now here we are going back into the era of 20 years ago. We’re going to have not only Roundup, but we’re going to have 2,4-D, dicamba, and there are going to be others. That just magnifies the management and application issues,” he tells CropLife® magazine.
Wolf worked with Monsanto in the 1990s when it first introduced Roundup Ready crops on how to solve drift issues, which pale in comparison to those we face today, he says, as the two new mega-technologies from Dow AgroSciences (Enlist Duo) and Monsanto (Roundup Ready Xtend) close in on their launches.
For Dow’s Enlist Duo, EPA has put in place restrictions to avoid pesticide drift, including a 30-foot in-field “no spray” buffer zone around the application area, no pesticide application when the wind speed is over 15 miles per hour, and only ground applications are permitted. The 2,4-D formulation contains choline salt that is less prone to drift and volatilization than amine or ester formulations, says Dow.
Monsanto’s Roundup Ready Xtend dicamba system, which is nearing registration and will be ready for the 2017 season, carries on the draft label a formidable 110-foot buffer zone, with some exceptions including paved roads, non-sensitive areas, and wheat. Its XtendiMax stand-alone dicamba formulation also requires non-ammonium sulfate (AMS) water conditioners — removal of the ammonium sulfate is designed to minimize dicamba volatility. Monsanto expects the final label to differ from the draft label after the EPA weighed data submitted during the public comment period.
Yet no matter how dramatic the improvement of the formulation and adjuvant used, no one drift management strategy can or should be relied upon. “You can put drift control into the tank but that doesn’t excuse some of the other things you might do. It all works together,” says Wolf, who stresses, “If more is going into the target, less should be drifting. That’s what it’s all about. Application is the key.”
Wolf trains applicators in BASF’s On Target Application Academy, which he helped to develop, and is gearing up to start incorporating field driving techniques — he has gotten feedback that more help is needed in educating younger, more inexperienced applicators.
As he drives across the country to various events and courses, he records the locations of fields he passes, and captures the images on Google Earth. With those images he will challenge course participants to figure out how to spray each field. It’s a way to demonstrate that not all fields are perfect rectangles like in parts of Illinois.
Higher Pressure Critical
“(Applicators need to learn) how to handle current scenarios that are out there, let alone the new scenarios with buffer zones and sensitive concerns,” Wolf says.
Nozzles will be specified on the labels, and all will create bigger-size droplets aimed at mitigating drift. Monsanto and BASF’s label singles out use of the Turbo TeeJet Induction nozzle.
Wolf emphasizes that employing higher pressure will be critical in the application process. In the past, it was common to associate low pressure with less drift, but because today’s nozzles are drift-reducing by engineering, lowering the pressure may reduce the pattern, enlarge droplets and thereby reduce coverage, he says. “We need high pressure to get the proper pattern and to get droplets suitable for coverage.”
Boom height is a big center of focus for good reason. The rule of thumb is that the spacing of the nozzle on the boom should be equal to the height of the boom or the nozzle above the target, and the target should be a growing canopy. A 20-inch boom, for example, means the boom should be around 20 inches above the target. “Geometry figures in, because the angle of the spray intersects with the nozzles beside it to form a uniform pattern. When the boom gets higher or gets lower, it affects the uniformity of the application. The one-to-one rule comes from that basis,” says Wolf.
The higher the boom, the more exposed it is to wind, increasing drift potential. When booms are higher, applicators tend to drive faster to keep from hitting the ground. When they go faster, the pressure gets higher, droplets get smaller, and drift potential rises.
“If he drifts he’s inefficient, and that product moves off target and causes damage, and that’s an increasingly high expense depending on the level it gets to,” including costly drift litigation, which Wolf knows about firsthand as an expert witness.
Better Records
He recalled a case on which he served as an expert witness in Kansas several years ago, where a local grower had taken six years to get to production on a five-acre patch of grapes. A neighboring farmer took him out in one spray operation.
A piece of advice from his time spent on the legal side? Keep better records. “We need to write down nozzle type, spray pressure, speed, and all the details of an application that currently I think more people are starting to do, and in my opinion, are going to have to.” Wind speed and direction should also be recorded multiple times during the job, he adds.
Ag retailers with large service areas should also observe weather conditions and sensitive crops downwind. Wolf has seen an issue with applicators being sent out to spray fields on 40- to 50-mile trips — a distance over which weather can change dramatically and which discourages an applicator from turning back in subpar conditions.
The new technologies, to be sure, are a tremendous asset for controlling hard-to-kill and resistant weeds. “The challenge is to get the application world in tune the way it’s going to take to be good stewards,” Wolf says.